Rolling Mill Automation Training Course
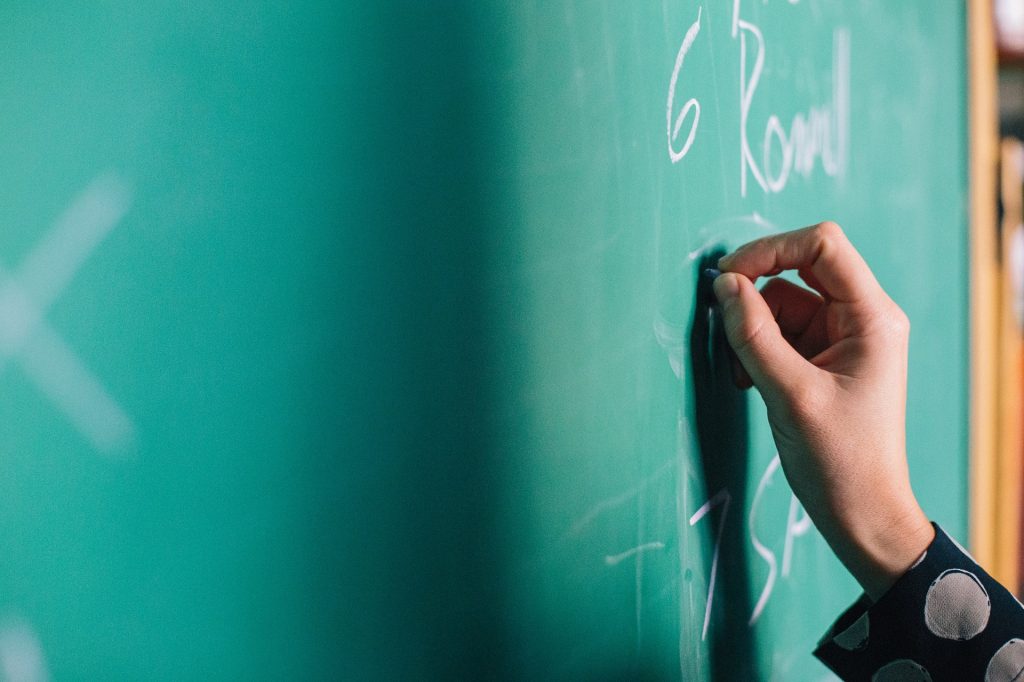
Course Description
TelePro periodicallly offers a rolling mill automation technology training program at its offices in St. Charles, Illinois. The program is a detailed treatment of mill automation system design and practical, real-world implementation issues. Single-stand and tandem mill applications in both hot and cold rolling are covered. The target audience includes engineers, technologists and technical managers involved in the specification, evaluation, implementation, management, maintenance and/or support of rolling mill automation systems.
Program duration is approximately 36 hours over four and a half days, beginning on a Monday morning and finishing at noon Friday. The program will be presented at the training center at TelePro's office in St. Charles, Illinois. It will cover the following topics (a complete outline is presented in Section 2 below):
- Common rolling mill geometries and actuator configurations
- Rolling process physics overview
- Roll gap modeling for control: force, torque and extrusion
- Strip profile, shape and flatness: definitions, interactions and modeling for control
- Design of non-interactive thickness and tension control
- Design of shape control
- Design of profile control
- Model-based mill setup systems
- Case study: Actual mill automation project
Lecture material will be reinforced with hands-on workshops using TelePro's rolling mill simulation software.
The automation technology presented in this program is mathematically-based and derived from first-principles models of rolling process physics. The program will include modeling of rolling process mechanics: roll bite mechanics, roll stack behavior and material properties. Control algorithms will be derived from the resulting mathematical process models.
Participants should have a general understanding of the following:
- Basic mechanics: friction, pressure, force, torque
- Basic algebra
- Basic geometry
Prior rolling mill control experience is beneficial, but not required.
Schedule and Cost
The next training course has not yet been scheduled. Please contact us if you are interested.
The cost per person for the training program is summarized in the following table:
Description | Cost |
1-3 participants from the same company | $4,500/ea. |
Additional participants from the same company | $1,500/ea. |
This cost includes:
- Four and a half days of training lectures and hands-on workshop sessions
- Course notes and presentation copies
- Lunches and refreshments
- Program dinner
Reservations can be cancelled with full refund up to 4 weeks prior to the beginning of the course; after this time deposits will not be refunded but can be applied to a future training course.
Course Outline
The program outline is as follows:
- Rolling Mill Configurations
- Common Roll Stack Geometries
- 2-High Mills
- 4-High Mills
- 6-High Mills
- Cluster Mills
- Roll Deflection and Crown Control
- Roll Bending
- Roll Crossing
- Variable Crown Side-Shifting Rolls
- Inflatable-Crown Rolls
- Rolling Process Physics
- Conservation of Mass Flow
- Mill Stretch and Hooke's Law
- Elongation, Strain and Tension Stress
- Roll Deflection
- Roll Crown
- Roll Flattening
- Roll Bite Mechanics
- Contact arc length
- Deformed roll radius
- Thickness variation through the roll gap
- Friction conditions
- Neutral angle and extrusion
- Roll gap pressure distribution
- Common Roll Stack Geometries
- Roll Gap Process Models
- Force
- Torque
- Extrusion
- Material Properties
- Strip Profile, Shape and Flatness
- Definitions
- Interactions: Roll Gap Profile, Strip Profile, Shape and Flatness
- Profile and Shape Modeling
- Design of Thickness and Tension Control
- Linearized Roll Gap Process Models
- Actuator Influences
- Non-Interactive Thickness and Tension Control Network
- Actuator networks
- Schedule-dependent actuator gains
- Dynamic response matching
- Control Algorithms
- PID feedback AGC
- Delay-compensating feedback AGC
- Feedforward AGC
- Mass-flow AGC
- Cyclical Disturbance (Eccentricity) Compensation
- Thread-mode interstand tension control
- Run-mode interstand tension control
- Complete System Examples
- Single-stand cold mill
- Two-stand cold mill
- Six-stand hot mill - conventional slab
- Three-stand hot mill - continuous cast slab
- Design of Shape Control
- Shape Control Actuators
- Shape Feedback Devices
- Calculation of Shape Sensitivities
- Disturbances
- Control actuators
- Error Signal Processing
- Symmetric Control
- Asymmetric Control
- Zone Cooling Control
- Feedforward Control
VII. Design of Profile Control
- Profile Control Actuators
- Profile Feedback Devices
- Calculation of Roll Gap Profile Sensitivities
- Disturbances
- Control Actuators
- Profile Changes vs. Shape Changes
- Initial Mill Setup
- Error Signal Processing
- Symmetric Control
- Asymmetric Control
- Zone Cooling Control
- Feedforward Control
VIII. Model-Based Mill Setup Systems
- Setup Strategy
- Rolling Practice Specifications
- Gap Setup
- Speed Setup
- Shape and Profile Setup
- Model Adaption
- Roll force model
- Roll gap model
- Thermal crown model
- Case Study: Three Stand Hot Continuous Mill